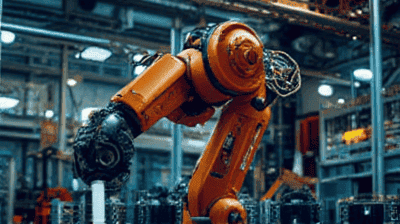
In the realm of modern manufacturing, industrial robots have become essential components on the factory floor, driving efficiency, productivity, and precision. As technology continues to advance at an extraordinary pace, these machines are not only evolving in terms of their capabilities but also becoming remarkably smarter. The integration of artificial intelligence, machine learning, and advanced sensors is revolutionizing the way industrial robots operate, opening doors to a new era in manufacturing.
The Evolution of Industrial Robots
To understand where industrial robots are headed, it is essential to look back at their evolution. The journey of industrial automation began in the late 20th century and has since undergone significant transformations.
Early Days of Industrial Robots
The introduction of the first industrial robots can be traced back to the 1960s. One of the pioneering models was the Unimate, developed by George Devol and later used in General Motors factories for tasks such as welding and material handling. These early robots were simple mechanical arms capable of performing repetitive tasks but lacked versatility and intelligence.
Advancements in Robotics
As technology progressed, industrial robots began incorporating more sophisticated features, including:
Programmability: Early robots required extensive programming for each task, limiting their flexibility. The introduction of programmable logic controllers (PLCs) allowed for more straightforward programming and reprogramming of robots for different tasks.
Increased Payload and Reach: New designs enabled robots to handle heavier loads and reach greater distances, making them more suitable for a wider array of applications.
Sensor Integration: Sensors began to be integrated into robots, providing them with the ability to perceive their environment and respond to external stimuli.
Collaborative Robots (Cobots): The emergence of collaborative robots marked a significant shift in industrial robotics. Cobots are designed to work alongside humans safely, enhancing human capabilities without the risks associated with traditional industrial robots.
Current State of Industrial Robots
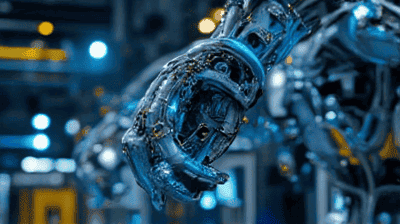
Today, industrial robots are a vital part of manufacturing processes across various industries, including automotive, electronics, consumer goods, and pharmaceuticals. Their applications include assembly, welding, painting, material handling, and quality inspection.
Types of Industrial Robots
Industrial robots can be categorized into several types based on their design and applications:
Articulated Robots: These robots have rotating joints and are highly versatile, making them suitable for tasks like welding, painting, and assembly.
SCARA Robots: Standing for Selective Compliance Assembly Robot Arm, SCARA robots are ideal for assembly tasks that require precision and speed.
Delta Robots: Known for their parallel link design, delta robots excel in high-speed picking and packaging applications.
Cartesian Robots: Also known as gantry robots, these operate on three linear axes and are typically used in CNC machinery.
Collaborative Robots: Cobots work alongside human operators, designed with safety features that allow them to operate in close proximity to people.
The Role of Artificial Intelligence in Industrial Robots
One of the most significant advancements driving the future of manufacturing is the integration of artificial intelligence (AI) into industrial robots. AI enables robots to perform tasks that require learning, reasoning, and adaptation, thereby enhancing their efficiency and capabilities.
Machine Learning
Machine learning, a subset of AI, allows robots to improve their performance through experience. By analyzing historical data and performance metrics, robots can learn from past actions, refine their decision-making processes, and optimize their operations.
Applications in Manufacturing
Predictive Maintenance: AI-powered robots can analyze sensor data to predict when a machine is likely to fail or require maintenance. This proactive approach reduces downtime and minimizes costs associated with unexpected breakdowns.
Process Optimization: By continuously monitoring production processes, AI algorithms can identify inefficiencies and recommend adjustments. This leads to optimized workflows and reduced operational costs.
Quality Control: Advanced vision systems, integrated with AI, enable robots to perform real-time quality inspections. They can detect defects and inconsistencies with greater accuracy than humans, ensuring higher product quality.
Perception and Vision Systems
The integration of advanced perception systems, including camera technologies and machine learning algorithms, allows robots to understand and interpret their surroundings more effectively.
Computer Vision: Robots equipped with computer vision can recognize objects, interpret spatial relationships, and interact with their environment. This capability is crucial for tasks such as picking, sorting, and assembly.
Depth Sensing: Using technologies like LiDAR and stereo cameras, robots can perceive depth, allowing for better navigation and obstacle avoidance in complex environments.
Natural Language Processing
Natural language processing (NLP) is another AI advancement that enables humans to communicate with robots using natural language. This facilitates easier programming and interaction, as operators can issue commands verbally instead of through complex programming interfaces.
Collaborative Robotics: Working Hand in Hand with Humans
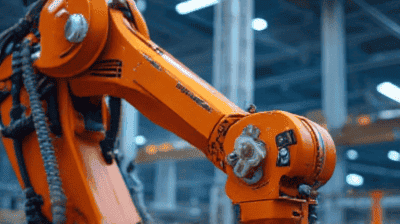
The rise of collaborative robots (cobots) marks a significant shift in how humans and robots interact in manufacturing environments. Cobots are designed to assist human workers, enhancing productivity while ensuring safety.
Key Features of Collaborative Robots
Safety Systems: Cobots are equipped with safety sensors that allow them to detect human presence and halt operations automatically, minimizing the risk of accidents.
Ease of Use: Many cobots feature intuitive interfaces and can be programmed with minimal training, allowing non-experts to deploy and operate them effectively.
Flexible Deployment: Cobots can be easily reprogrammed and moved between different tasks and workstations, providing flexibility in manufacturing operations.
Applications of Collaborative Robots
Cobots have found applications across various manufacturing processes:
Assembly: Cobots can assist in assembling products by performing repetitive tasks while humans handle more intricate work.
Material Handling: Cobots can lift and transport materials, reducing the physical strain on human workers while increasing efficiency.
Quality Inspection: By complementing human inspectors, cobots can perform initial quality checks, allowing humans to focus on more complex evaluation tasks.
Smart Factories and Industry 4.0
The concept of Industry 4.0 represents the next phase of manufacturing, characterized by the digitalization of processes and the integration of smart technologies. Industrial robots play a crucial role in this transformation.
Key Elements of Industry 4.0
Internet of Things (IoT): By connecting machines and systems to the internet, manufacturers can gather real-time data, enabling better decision-making and process optimization.
Big Data Analytics: The vast amounts of data generated by connected devices can be analyzed to derive insights, identify trends, and improve performance in manufacturing operations.
Automation and Artificial Intelligence: The synergy between automation and AI enhances operational efficiency, enabling demand-driven production and adaptive manufacturing processes.
The Emergence of Smart Robots
Smart robots equipped with IoT capabilities and AI algorithms can communicate with each other and with central control systems. This interconnectedness allows for:
Autonomous Decision-Making: Smart robots can analyze data in real-time and make decisions without human intervention, improving response times and operational efficiency.
Adaptive Manufacturing: Robots can dynamically adjust their operations based on real-time demand, minimizing waste and ensuring optimal resource utilization.
Remote Monitoring and Management: Cloud-based platforms enable manufacturers to monitor robot performance and production processes remotely, facilitating proactive management and optimization.
The Impact of Smart Industrial Robots on the Workforce
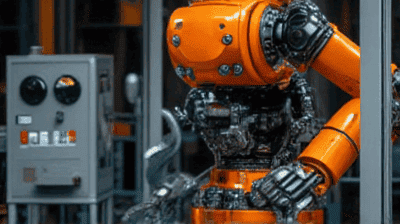
As robots become smarter and more integrated into manufacturing processes, concerns about their impact on the workforce arise. While there is apprehension about job displacement, it is essential to recognize the transformative potential of these technologies.
Job Transformation, Not Replacement
Smart industrial robots are likely to change the nature of work rather than eliminate jobs entirely. While some repetitive and physically demanding jobs may be automated, new roles will emerge that require human intelligence, creativity, and problem-solving skills.
Upskilling and Reskilling: Workers will need to acquire new skills to work effectively alongside robots and leverage advanced technologies. Upskilling initiatives and training programs will be vital to prepare the workforce for future demands.
New Job Creation: The integration of smart robots will create new job opportunities in areas such as robotics engineering, data analytics, and system maintenance.
Collaboration Over Competition
The future of manufacturing will likely focus on collaboration between humans and robots. By combining human ingenuity and oversight with robotic efficiency and precision, manufacturers can achieve higher levels of productivity and innovation.
Challenges Ahead
Despite the tremendous potential of smarter industrial robots, challenges remain in their implementation and adoption.
Technical Challenges
Integration Complexity: Integrating advanced robotic systems into existing manufacturing processes can be complex and require significant investment in infrastructure and training.
Data Security: As manufacturers embrace interconnected systems, data security concerns arise. Ensuring the protection of sensitive information and preventing cyber threats becomes essential.
Economic Factors
Cost of Implementation: While the long-term benefits of robotic automation are evident, the initial costs associated with adopting smart robots can be a barrier for some manufacturers.
Return on Investment: Companies need to evaluate the return on investment for robotic implementation carefully. Analyzing production rates, operational efficiency, and labor costs is crucial in making informed decisions.
Regulatory Considerations
As robotics becomes more prevalent in manufacturing, regulatory frameworks will need to evolve to address safety, liability, and employment concerns. Policymakers will play a vital role in ensuring that regulations promote innovation while safeguarding workers' rights and well-being.
The Future Outlook
The future of manufacturing powered by smarter industrial robots is bright and full of potential. As technology continues to evolve, we can anticipate several trends shaping the landscape of manufacturing.
Increased Autonomy and Intelligence
Gardened by advances in AI and machine learning, industrial robots will become increasingly autonomous, capable of learning and adapting to new contexts without explicit programming. This evolution will enable them to tackle complex tasks in dynamic environments.
Greater Focus on Sustainability
Sustainability will be a central theme in the future of manufacturing. Smart robots can optimize resource usage, reduce waste, and facilitate sustainable practices, contributing to the overall goal of environmentally friendly manufacturing.
Global Collaboration and Innovation
As robotics technology advances, collaboration between researchers, manufacturers, and technology providers will foster innovation. Open-source platforms and collaborative research initiatives will help accelerate developments in smart robotics.
Enhanced Human-Robot Collaboration
The future will see closer collaboration between humans and robots, where each complements the other's strengths. This partnership will empower workers, enhance productivity, and lead to exciting developments in manufacturing processes.
Conclusion
The future of manufacturing is poised for transformation as industrial robots become smarter, more autonomous, and increasingly integrated into production processes. The advancements in AI, machine learning, and sensor technologies are paving the way for a new era of efficiency, precision, and innovation.
As we embrace the potential of smart industrial robots, it is crucial to navigate the challenges associated with their implementation and adoption. By focusing on collaboration, upskilling the workforce, and fostering a culture of innovation, the manufacturing industry can harness the power of technology to create a more sustainable, efficient, and prosperous future.